The Significance of Plastic Impellers in Submersible Pumps
In the realm of fluid management and engineering, submersible pumps have emerged as a vital tool for various applications, from industrial processes to domestic water supply systems. A key component that significantly influences the efficiency and performance of these pumps is the impeller. In recent years, plastic impellers have gained substantial traction in the submersible pump industry due to their unique attributes.
A submersible pump, as the name suggests, is designed to operate underwater, often in harsh conditions that demand resilience and durability. The impeller, the rotating part of the pump responsible for moving fluid, plays a pivotal role in this process. It converts the mechanical energy from the motor into hydraulic energy, propelling the fluid through the pump's discharge port.
Traditionally, impellers were made from metals like cast iron or stainless steel, known for their strength and durability. However, plastic impellers have challenged this norm with their lightweight, corrosion-resistant, and cost-effective properties. Materials like Polypropylene (PP), Polyvinyl chloride (PVC), and Acrylonitrile Butadiene Styrene (ABS) are commonly used for manufacturing plastic impellers due to their resistance to chemical attack and excellent wear characteristics.
One of the significant advantages of plastic impellers in submersible pumps is their ability to handle corrosive fluids. Unlike metal impellers, plastics do not corrode or rust, making them ideal for applications involving acidic or alkaline liquids. This not only extends the lifespan of the pump but also reduces maintenance costs This not only extends the lifespan of the pump but also reduces maintenance costs
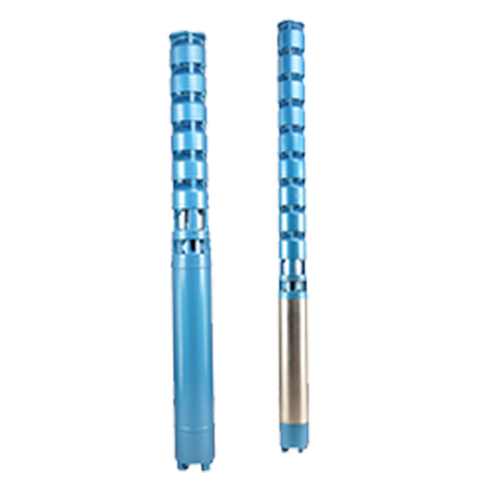
This not only extends the lifespan of the pump but also reduces maintenance costs This not only extends the lifespan of the pump but also reduces maintenance costs
submersible pump plastic impeller.
Furthermore, plastic impellers offer superior resistance to erosion caused by abrasive particles in the fluid. They are less prone to damage, ensuring consistent performance over time. Their lightweight nature also contributes to lower power consumption, enhancing the overall efficiency of the pump.
Additionally, plastic impellers are easier to manufacture, allowing for more intricate designs that can optimize flow dynamics and enhance pump performance. They can be molded into complex shapes, enabling better fluid management and potentially higher pressure capabilities.
Despite these benefits, it is crucial to note that plastic impellers may not be suitable for all high-pressure or high-head applications where metal impellers still reign supreme. However, for many general-purpose and specialized applications, plastic impellers in submersible pumps have proven to be a game-changer, offering a balance between functionality, durability, and cost-effectiveness.
In conclusion, the use of plastic impellers in submersible pumps has revolutionized the industry by providing a versatile solution that addresses specific operational challenges. As technology continues to advance, we can expect further innovations in plastic impeller design, improving the efficiency and reliability of submersible pumps even further.